INDUSTRY-LEADING QUALITY
At WhiteWater, we always endeavour to perfect processes and upgrade materials as part of our commitment to continuous improvement—it’s because of this we’re able to build our water slides with the best fiberglass in the industry.
AWARD-WINNING SILKTEK™ FIBERGLASS
The winner of IAAPA’s Brass Ring Award, WhiteWater’s SilkTek™ fiberglass uses the RTM process to engineer opaque and translucent fiberglass that is fade-resistant and long-lasting. When combined with our innovative Gel Coat, with its built in top coat, our fiberglass is brighter, smoother and less susceptible to peeling and delamination, even years after install.
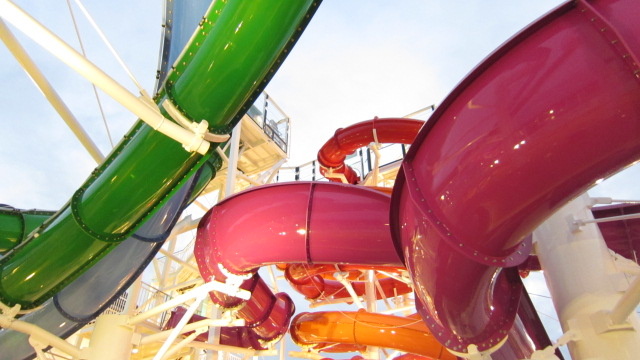
STRINGENT TESTING
From our Center of Excellence in Vancouver, Canada, our experienced team of engineers test all our fiberglass in the most extreme of conditions to prevent against peeling and colour fading. It is from these tests that we develop our strict standards, which we then roll out to our global manufacturing plants to ensure consistency of results.
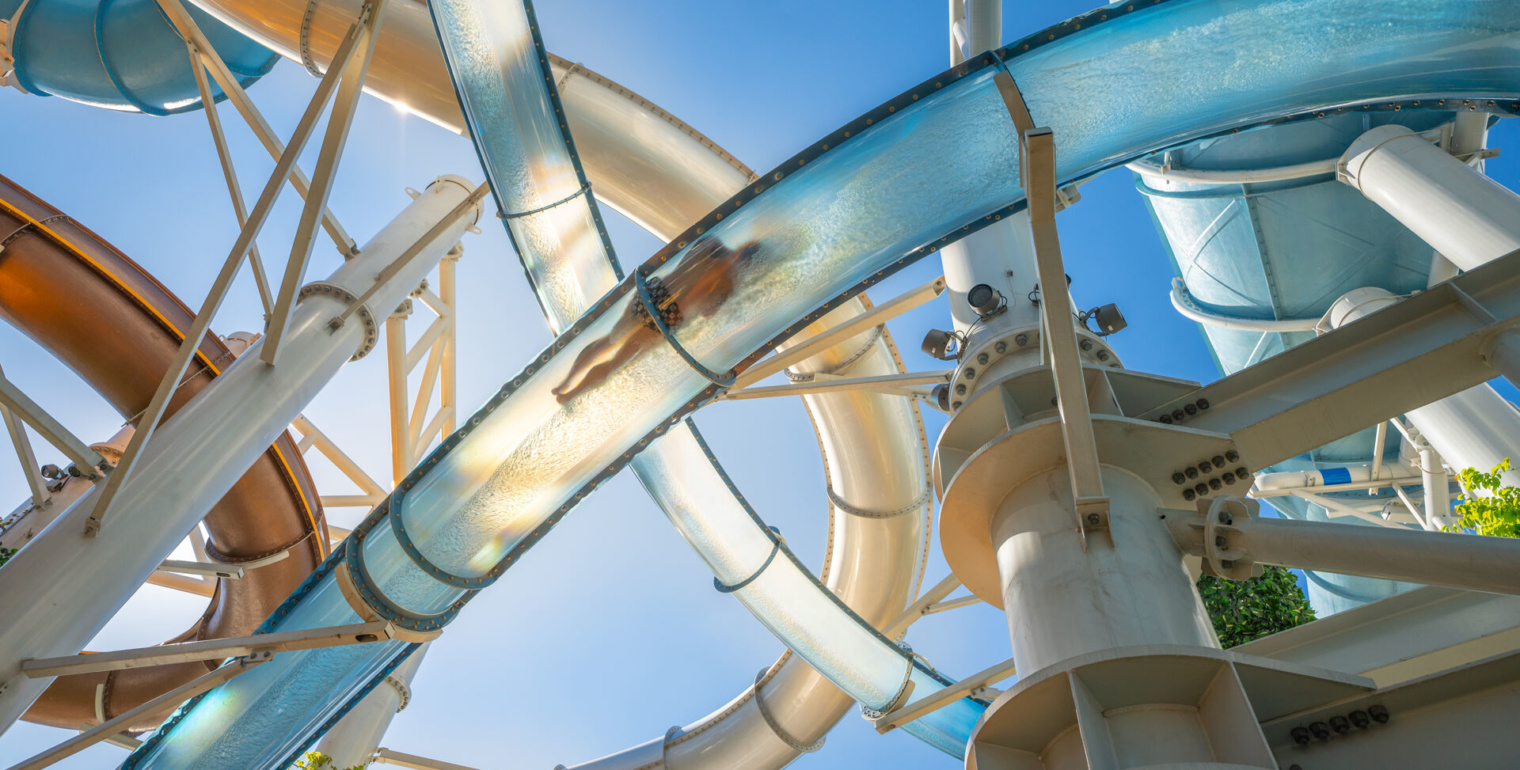
LOCAL FOR LOCAL
It is from these tests that we develop our strict standards, which we then roll out to our three global manufacturing plants to ensure consistency of results.
Our international plants located in Europe, Asia, and North America mean that we can reduce shipping times and costs, to serve our clients more effectively and efficiently.
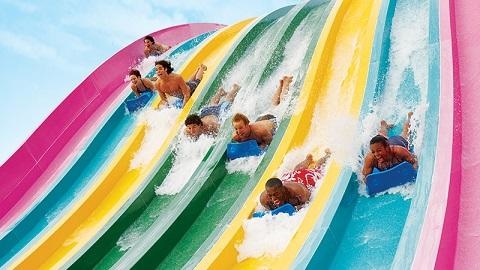
PROCESS MATTERS
There are a range of manufacturing processes when it comes to water slide fiberglass—the gold standard being Resin Transfer Moulding. At WhiteWater, we offer three options, depending on the slide:
• Resin Transfer Moulding
• Vacuum Assisted Resin Transfer Moulding
• Open Mould Layup
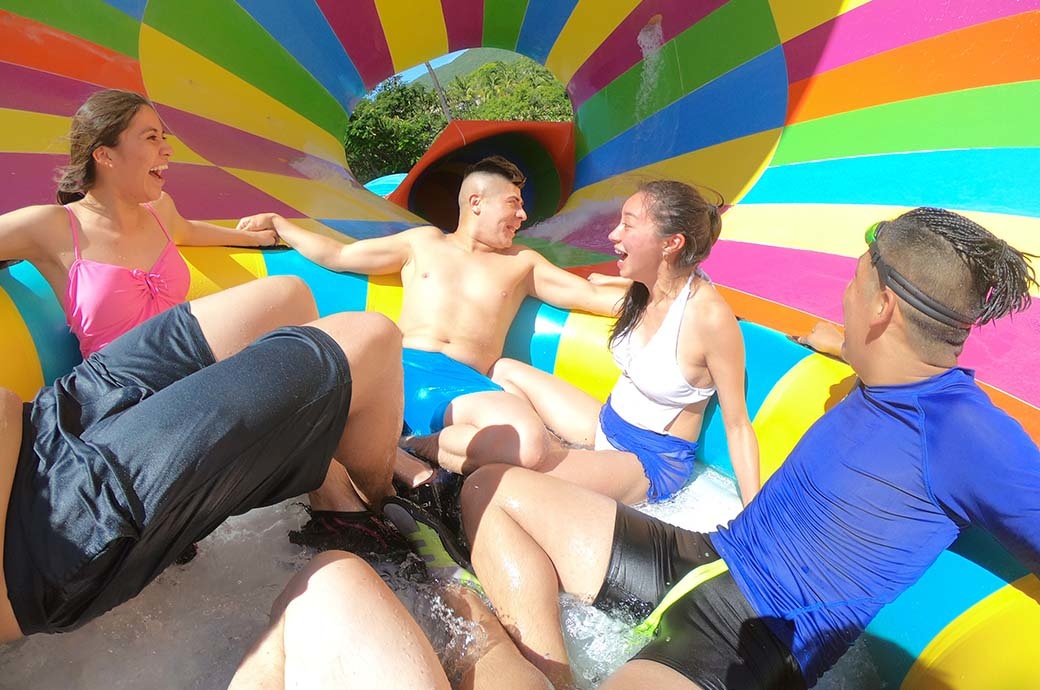
Resin Transfer Moulding
The premier process for making water slide fiberglass is now Resin Transfer Moulding, also known as RTM. A more advanced type of manufacturing resulting in fiberglass that is smooth on both sides, consistent in thickness, and the same strength qualities throughout the slide. Moreover, the process of making RTM is less labour intensive and better for the environment as the styrene emission is much lower than the Open Mould method and results in less physical waste than conventional methods.
Reusable Vacuum Membrane Moulding
Offering the best of both Open Mould and RTM, the silicone bagging method within a reusable vacuum membrane molding makes it easier to create parts that have a double curvature and require a mould lock. This makes parts like transitions, entry boxes, and runout lanes a good candidate for the reusable vacuum membrane moulding method.
Open Mould
The original process to make water slide fiberglass, Open Mould fiberglass is smooth on the ride surface while rough on the non-ride surface. Low volume, labour intensive, and high waste yields make Open Mould better suited for large components. The percentage of our Open Mould production is increasingly reducing as most clients tend to favour the look and advantages of the resin transfer moulding process.
Find inspiration for ways in which parks can upcycle their water slides into new uses!
Download the Quick Guide