
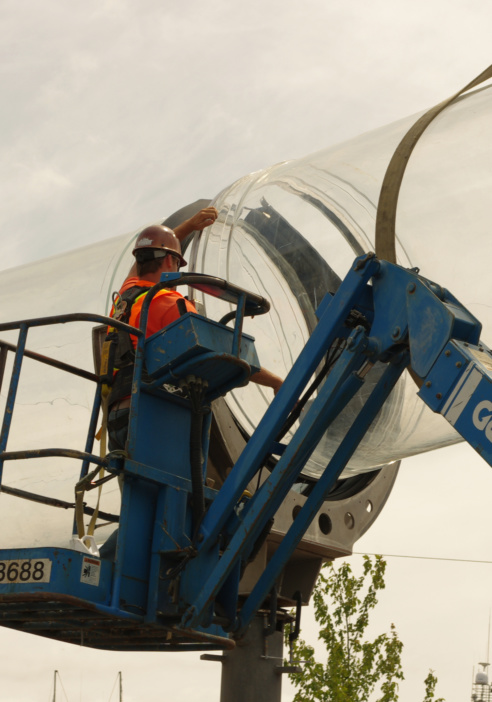

How to Create a Successful Water Park – Part 3: Installation
After attractions have been carefully engineered and manufactured, the rides are then sent to the park’s construction site into the hands of WhiteWater’s installation team. Whether they are building a standalone water park, an extension onto a theme park, or a brand-new project on land or a cruise ship, these team members are experts in flying fiberglass into the air and bringing the sections together to create our industry-leading aquatic attractions. Digging into the installation phase, this week we sit down with two of our installers, Lee Mallozzi and Milko Cakic, to finish off our series on how to create a successful water park.
Putting the Pieces Together
To people outside of the theme park industry, it might seem like the construction of a water park comes together overnight. It is the culmination of months of hard work. Milko Cakic, one of WhiteWater’s Senior Install Advisors, revealed the secret recipe for installation in three main ingredients: planning, people, and support.
Plan
For installation supervisors, the work begins before they even step on site. A common practice for Lee Mallozzi, another Senior Install Advisor, is to look at the drawings while he is on the airplane so he can readily identify which sections of fiberglass should be assembled first. Planning can be difficult because each project is different, but the installers prepare as much as possible and apply best practices from their years of experience. While they can almost be assured that their plan will be changed, the goal is always the same: to build the attractions in the most efficient and safest way possible.
People
Once the installer arrives on site, they work with the surveyor to check the elevations of the concrete pedestals and take an inventory of the crates. After the surveyor gives them the “all clear,” the team will then begin to take the fiberglass out of the crates and organize them into different slide parts. From here, the magic begins, and the team starts to assemble the parts on the ground. This is where Milko’s second main ingredient to success comes in: the people. While joining the sections of the ride together, there might be conditions on site that become challenging. This is where people become an important part of the project because the right people can create a solution quickly and keep things moving.
Support
If issues do arise, support from the project management, designers, and mechanical teams are the last crucial component. Installers are the ones working face-to-face in front of the client, so it’s vital to have support from the rest of the team in getting information quickly. While sometimes it might feel like the installers are on their own, there’s a full group of knowledgeable professionals backing them up.
Adapting to Unique Site Conditions
Indoor Water Parks
While the installation teams have built water slides in over 90 countries around the world and across a plethora of unique venue types, there can still be some sites that surprise them. When this is the case, the team can sometimes get creative about how they build the water slides. This can be common in outdoor projects but is more frequently the case for indoor projects as the team needs to work within an existing building envelope. In one instance, Lee was constructing a water park inside a hotel that had only one suitable opening in the building so materials could only be brought in from one entrance. This meant that he had to get creative. Rather than building from the bottom up, the team constructed the attractions from the top down to more easily be able to bring the different components inside.
Cruise Ships
A floating water park is one of the most challenging projects for the team as they often have tight schedules and space constraints. On a cruise ship, the construction for each part takes place at the same time. So while our team might be installing water slides, furniture, and other items are also being lifted onto the ship. This requires the team to make a reservation, wait their turn to use the crane, and utilize protection techniques to make sure the fiberglass is safe while other people are moving about. Because the shipyard is also an entry point to the country, there are special safety parameters to be followed and documentation that needs to be filled out to get the full team onsite. These procedures can make getting materials onsite difficult as well.
Time to Ride: The Commissioning Process
Lee and Milko both emphasized how extensive the commissioning process is. At WhiteWater, we follow the highest global standards and follow rigorous safety protocols. Long before the installation team turns the water on, tests and simulations have been run to account for different weight classes. Once the water is running, there are a lot of different steps to take to make sure everything that has been done on the construction site over the past few months is as it should be. Commissioning should not be rushed. Different from rollercoasters, a water slide never has two rides that are completely the same due to the way the water moves and how a person is sitting on the raft or laying on the fiberglass. Because of this, the installers run a multitude of tests to make sure the ride is safe for every category of rider.
Following a checklist, the installers begin commissioning by inspecting all the structures and bolts. Then, there is a walkthrough of the slide to make sure it’s all good to go. During this step, the team crawls through the water slide and investigates all the joints to make sure that they are correct. Once all the safety and structural checks are done, the pumps are turned on and adjusted to the specified gallons per minute rate. Then the testing process begins.
Although the water is run, Lee doesn’t start riding right away. For example, on family rides, he likes to send an empty raft through and watch how it glides down the slide. After that, weight bags are added, and the team continues to run some more checks. After all the weight categories are signed off with bags, that’s when the riding begins! Lee would then jump on the raft with the park’s lifeguards or operations team and run the remaining testing to ensure all the O&M requirements are met.
Let’s Get Building
If you’re ready to get building, we would love to hear from you at whitewater@whitewaterwest.com.
Thank you for following along with our series of what it takes to create a successful water park! If you’re interested in staying up to date with the latest news and articles from WhiteWater, register for our newsletter and keep your eyes open for the next project announcement built by our talented installation team!