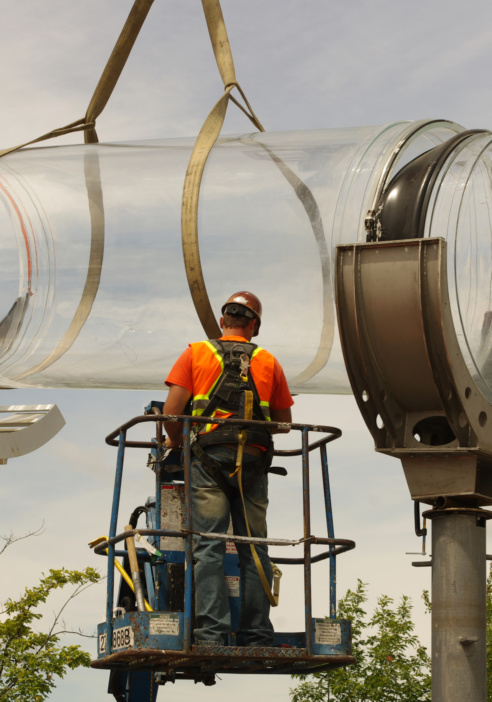
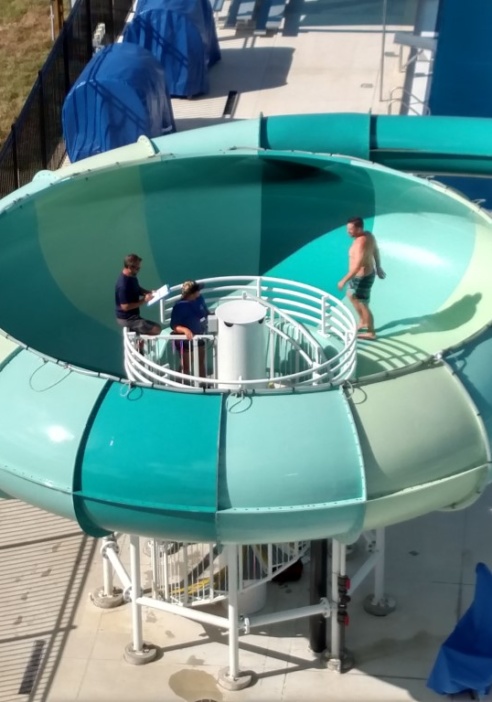

Moving into Action: The Importance of Using Your Operating Manual
Phase 1: Putting a Plan into Action
An office move is an exciting time for any company—employees collectively come together and look forward to the start of something new in a fresh, organized office. However, before the celebration can start, the office must endure the manual labor of picking up and physically relocating.
After an office move of our own, we learned firsthand how many things get uncovered that we didn’t know we had to begin with. From sculptures to awards, we uncovered a plethora of objects that would have been valuable to use and put on display, had we known of their existence.
Phase 2: Installation & Commissioning
An office move can be very similar to the process of commissioning a water slide. For example, during our move we worked with an external company to relocate from one location to another, sharing responsibilities. The testing and commissioning of a water slide follow a similar pattern; for example, during commissioning WhiteWater shares the safety and preopening with the client.
A WhiteWater Installation Advisor works on-site even before commissioning during the installation phase to confirm all of the materials have arrived on site, answer any technical questions the installation contractor might have, and ensure all of the equipment is assembled in accordance with WhiteWater’s engineering drawings and specifications. After a smooth installation, the client would then work on their portion of the deliverables; safeguarding that all the infrastructure equipment (pumps, water filtration, and water treatment plants) is operating correctly and that the necessary local government inspections have been completed.
After the slide has been installed and the client has done their portion of the work, our Installation Advisor would then return to site to perform a detailed inspection of the WhiteWater equipment. After an initial inspection, the Advisor would then take the equipment through the commissioning process checking the water flow, joints, and caulking. Advisors would also put the slide through a variety of weight class testing. Providing these tests all pass with flying colours, the attraction would then be ready for certification and the project manager would pass over the operating manual.
Phase 3: Putting the Operating Manual to Work
During the excitement of opening, it is not unheard of for a client to forget their interactions with their Project Manager and lose track of their operating and maintenance (O&M) manual. While we understand that this time can be busy and distracting, it is essential to keep the O&M manual accessible and implement the procedures inside of it as it includes important information for both the operators and their employees. Stick with us as we dive deeper into the pros of the O&M manual and help you to evaluate whether you are getting the most use out of your manual.
*if you have lost your O&M please contact us immediately to receive a new copy.
Phase 4: Putting the Operating Manual to Work
1. Communicate Effectively
While customers are the key ingredient to the success of any water park, certain rules and procedures should be made clear for the park to function both efficiently and safely. For example, one of the main safety concerns are height and weight requirements. Operators should make sure the requirements are met by posting clear signage, training your staff, and providing tools to measure height and weight. These two parameters are important to keeping the rider/vehicle on the designed path.
2. Follow Operating Guidelines
One of the most important parts of a water slide is water flow. Water flow enables the slide to perform with the right speeds whether accelerating or decelerating and make for a smooth ride for your guest. Having a way to measure flow and checking it before, during, and after operation is important.
Related to this is maintaining proper water quality, the wrong quality can eat away at surfaces or deposit calcium, which can cause vehicles to slow down. Make sure to follow the procedures in your O&M manual to test for water quality and adhere to the maintenance guidelines to reduce or eliminate calcium deposits to keep your guests safe.
3. Mitigate Risk Management
Operators should regularly inspect your ride and maintain it per the O&M manual. Taking these extra actions at the beginning and end of your operating day can enable you to find an issue before someone is injured, which is one of the most effective forms of risk management.
We recommend implementing Mobaro, an easy-to-use application that can be downloaded to provide you with an audit trail. Mobaro details each person’s responsibilities and provides a checklist for your team to follow, ensuring everything gets done. The application helps to capture task completion with time stamps providing you with important documentation, should you ever need it, without the paperwork. WhiteWater clients are able to receive get Mobaro set up for their attractions for free and enjoy the license for four weeks.
4. Ensure Consistency
Written O&M manuals can take the guesswork out of day-to-day operations and ensure all your employees understand the processes, policies, and procedures associated with running the attraction. Essentially, your operating manual becomes a go-to source of knowledge for everyone in the company, ensuring consistency. Useful for your staff veterans who may need a quick review and your new workers who don’t know who to turn to to ask specific questions, the O&M manual provides the foundational knowledge to provide for your slide.
5. Extend the Life of Your Investment
While the operating manual outlines important safety guidelines such how to properly operate the attractions, the reading and understanding of your O&M manual should continue through to the last page. By reading the O&M manual all the way through, you can see that there is also a lot of maintenance guidelines about how to best care for your slide including how to properly clean, wax, and recaulk the slide joints. Following the O&M manual will help to preserve the look and performance of the slide, extending the life of your investment.
Phase 5: Celebrate Your Success
Step back and take a moment to appreciate the hard work your O&M manual has saved you. The best water park is a safe water park, and, with the proper execution and use of preventative maintenance, you provide yourself with the best assurance of safety, performance, and extended equipment life. By following the manual’s instructions, documenting routine inspections and complying with the recommendations, most maintenance mistakes can be avoided, resulting in cost savings.
To learn more about the importance of operating manuals or recover your hard copy that mysteriously disappeared, please send an email to our Director of Customer Service Harley Ensing at harley.ensing@whitewaterwest.com.