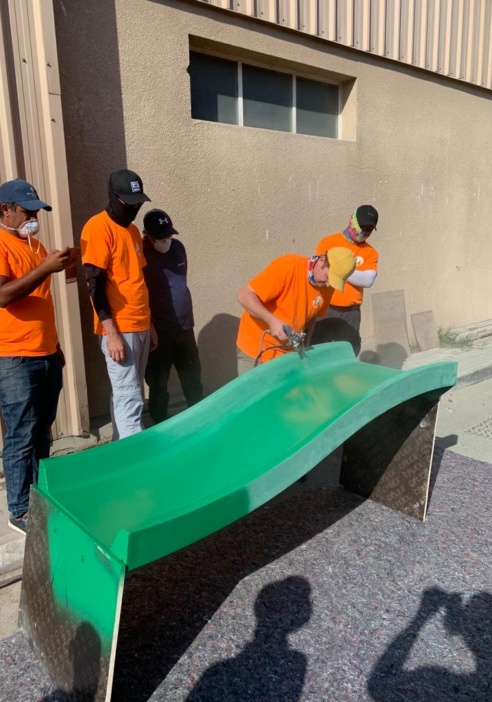
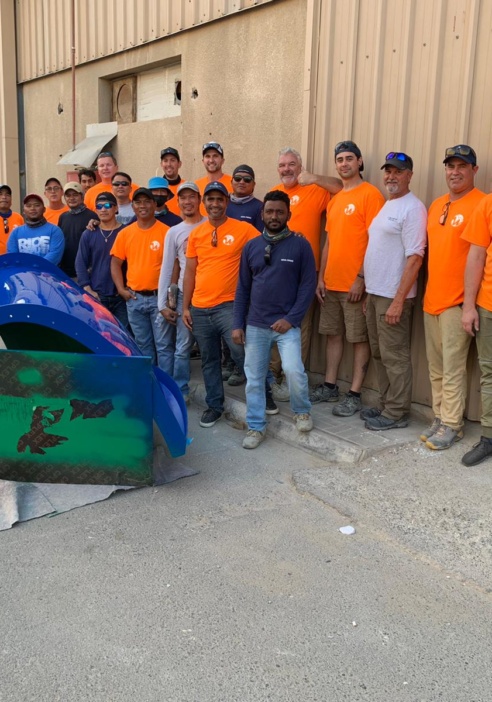
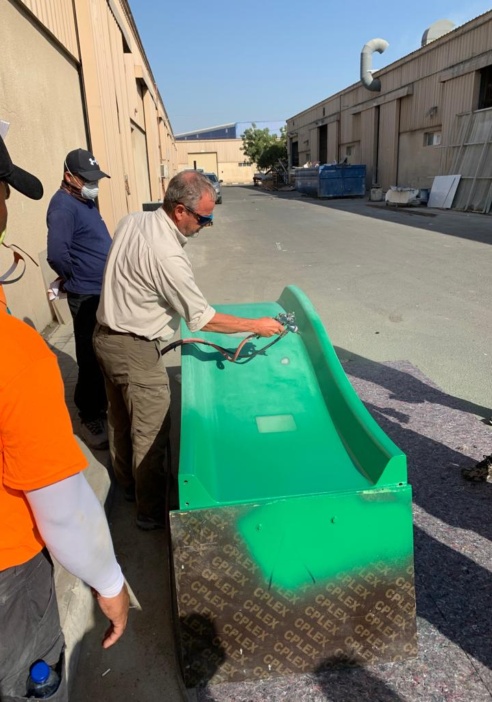
Spotlight: Water Park Maintenance and Support in the Middle East
The Middle East is a region synonymous with high expectations, where the tallest buildings, fastest attractions, and most luxurious hotels are the norm. Given these elevated benchmarks, it is critical that water parks here maintain their attractions to the highest possible standard. This is where WhiteWater’s Performance Services team comes in, providing specialized refurbishment services to ensure that water slides and aquatic play structures operate optimally and appear in their finest form. Let’s take a closer look at how WhiteWater has expanded and strengthened its maintenance and support department in this region to help partners like Wild Wadi Waterpark in Dubai with keeping their attractions looking—and functioning—great.
Developing Local Talent in the Region
When individuals are trained properly, they can perform their tasks efficiently and effectively. However, it’s not enough for each person to simply be good at what they do; success often depends on how well team members work together to achieve a common goal. It is under that mindset that Brian Vikner (Construction Operations Manager), Sean Conneely (Install Advisor), and Ray Sagasky (Team Development Specialist) put together a five-day training program in Dubai for 12 WhiteWater personnel and a handful of local resources to gather and learn from one another to make sure the right talent is available in the region.
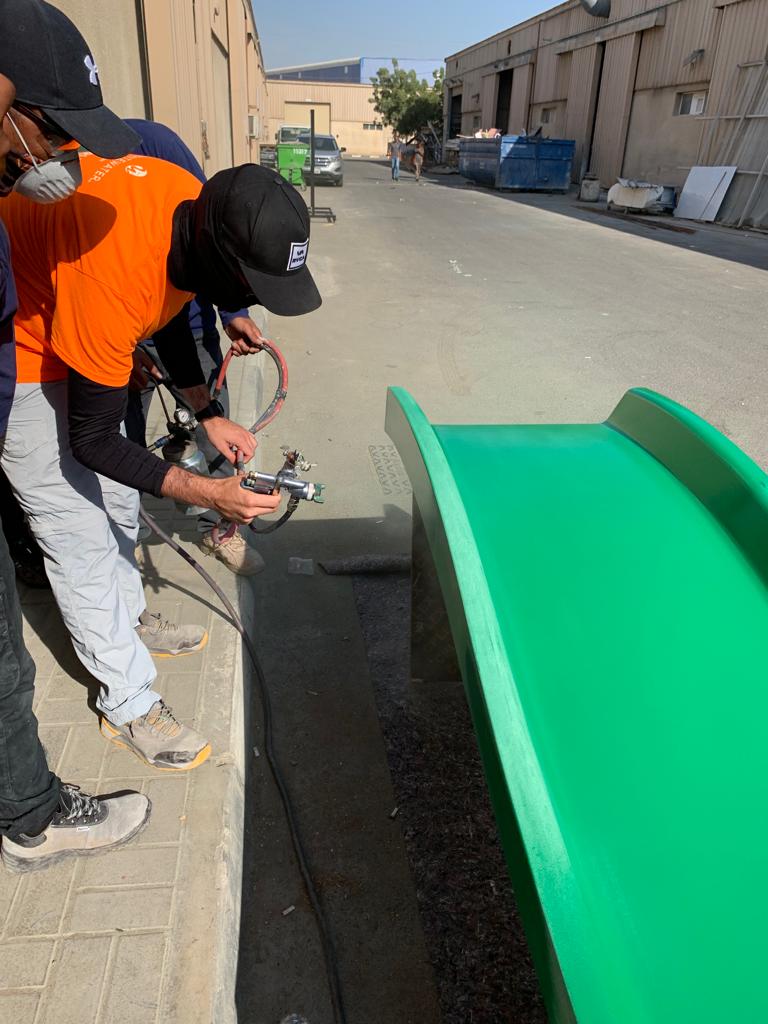
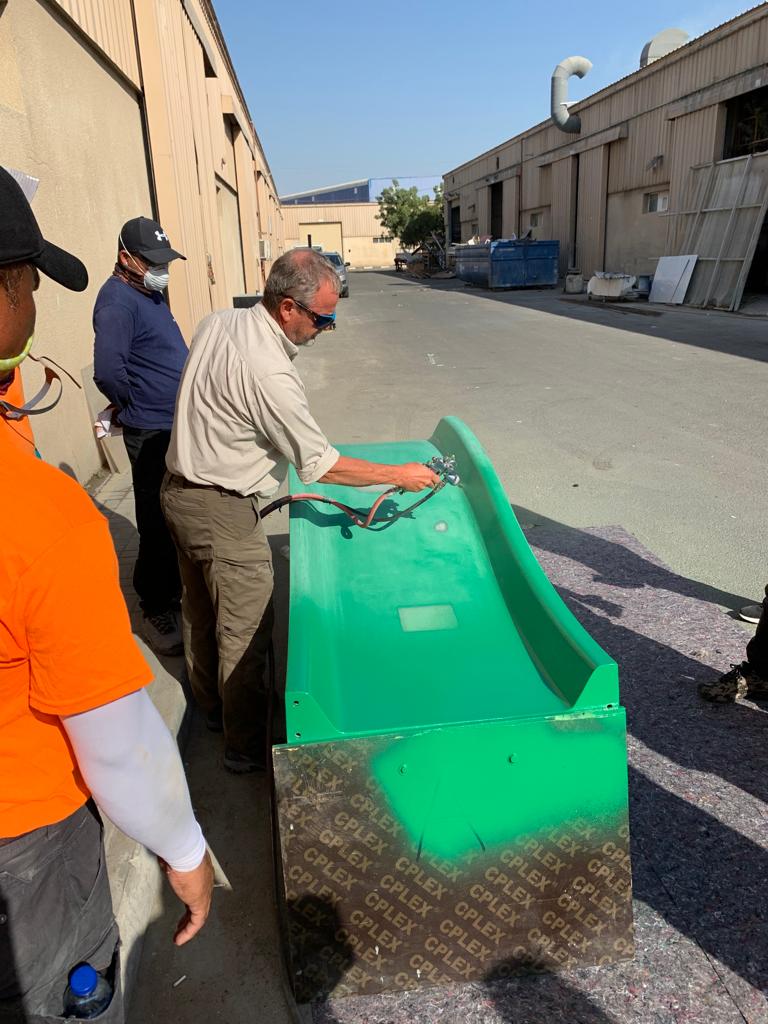
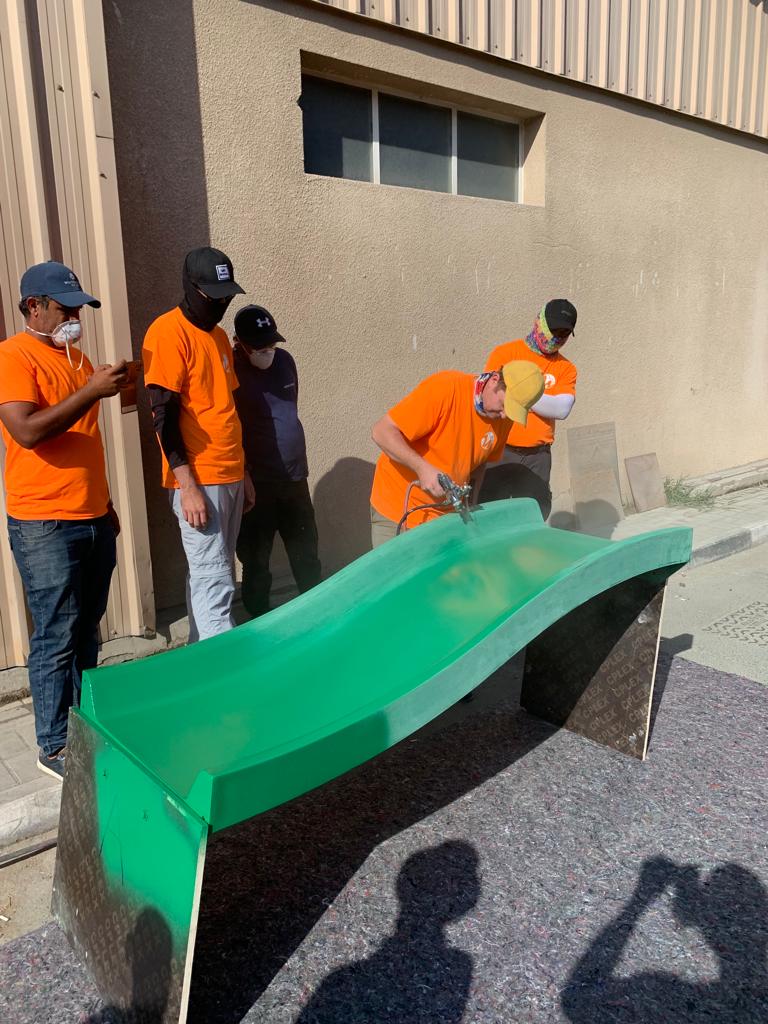
The participants adhered to the strict standards of the American Composites Manufacturers Association (ACMA), which follows the certified composites technician program procedures and processes. During this time, the group covered everything from basic fiberglass maintenance, such as scratch removals, to field repairs. To be able to identify the type of work needed, they looked at the integrity and aesthetics of the gel coat as well as the depth of the defect. The training also included:
- Handheld sprayers & professional gel-coat spray machines: how to reinstate the protective coating on the fiberglass and preserve structural integrity.
- Equipment overview and setup: analyzing the size of your repair and availability of materials.
- Surface prep and polishing: identifying the ideal time to perform maintenance and ensuring they have a solid foundation to begin repair.
(Featured from WhiteWater (orange shirts): Fredy Espiritu, Sean Conneely, Cris Donnan, Noel Atienza, Matthew Reilly, Brian Vikner, Ahmed Tarek, Ray Sagasky, Russell Thiebeau, Mark Hudon (white shirt), Ken Campbell, Oleg Zlenko)
Restore to OEM Finish: Water Slide Care at Wild Wadi Waterpark
Shortly after the training, the team was commissioned to help Wild Wadi with slide care on its RainFortress structure. The team was able to clean the different slides on the multi-level play structure and polish it up to a glossy shine within 12 days, taking advantage of the park’s scheduled downtime to revitalize the structure. Utilizing local resources in terms of supplies and manpower, WhiteWater saved the park money by removing the need to import materials or labour. WhiteWater’s team was extremely responsive and efficient, providing a high level of service that matched the expectations of the park’s guests.
The team doing the Wild Wadi repairs led by WhiteWater’s Matt Spurgeon, Noel Atienza, and Fredy Espiritu
Breathing New Life into the RainFortress
The team conducted both resurfacing and cleaning on Wild Wadi’s RainFortress. When faced with a resurfacing project, WhiteWater’s Performance Services team adopts a mechanical cleaning method using an orbital sander with various discs to remove old surface material in preparation for the application of new gel coat.
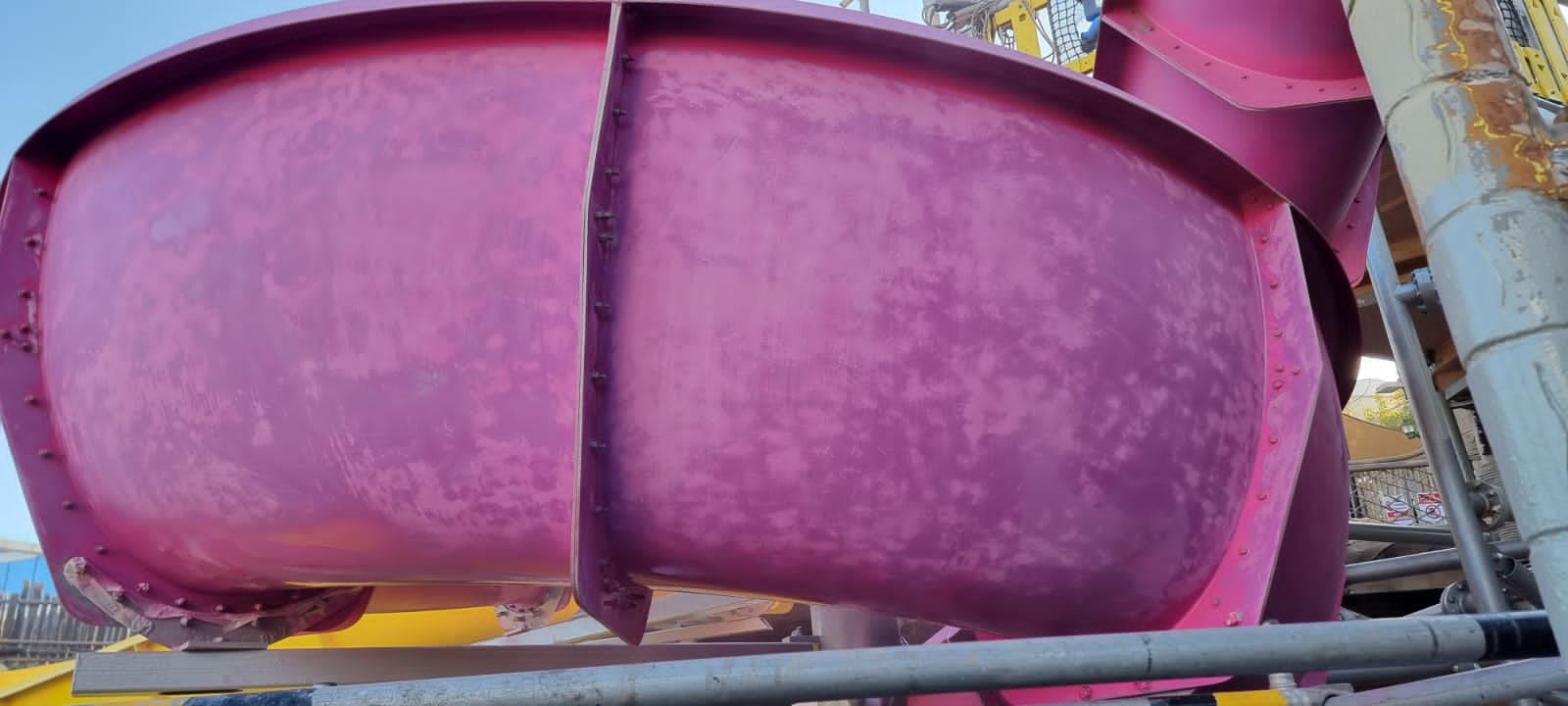
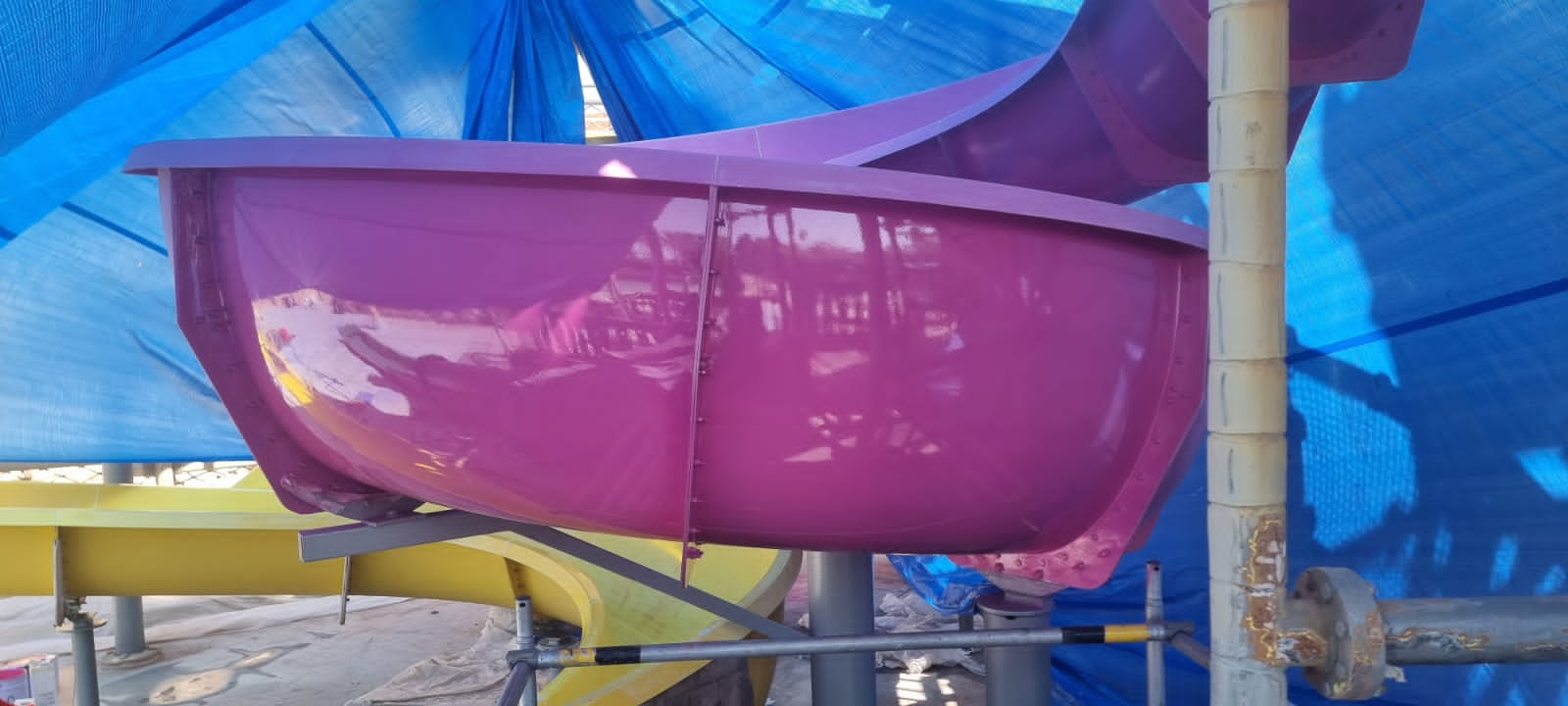
During the cleaning process, the team buffed the water slides with a fine-grit liquid compound to remove any imperfections from the gel coat surface. The mixture of standard pool chemicals when paired with the saltwater and sand in the air requires proper maintenance to prevent buildup on the slide path surface. This buildup, when left unchecked, can create a layer that feels like sandpaper on the fiberglass. For the final touch, the Performance Services team waxed the water slides to protect the gel coat that they had just cleaned.
“We were really impressed by the responsiveness of the WhiteWater team; we asked if they could support us, and it was as if the next day they were at the park with equipment. The level of detail and expertise provided matched the level of service our guests at Jumeriah expect, not leaving behind a single scratch on the slide. The reports made by the team were a nice supplement to the service provided and will help us not only plan our resources better but help in the upkeep of the attraction.” – Mohamed Hassan, Director of Operations, Wild Wadi
Supporting the Client After Completion
As the OEM, the team was able to create service reports during the restoration work with detailed recommendations according to the state of the attractions. Visibility is heightened after a slide is cleaned, enabling our experts to give advice or supply a budgetary number for future maintenance work. Like a strategic partner, these recommendations allow the water park to plan for support from Performance Services that might be needed in the future to keep its rides running in tip-top shape and make the equipment last longer.
Left: The team at the beginning of the resurfacing and cleaning. Right: The slide waiting for another round of gel coat midway through the cleaning process.
Water slides are assets that need to be taken care of, requiring attention and action to maintain quality and safety and extend their useful life. To get the most out of your water park equipment, contact WhiteWater’s Performance Services team to refurbish your water slides and aquatic play structures at whitewater@whitewaterwest.com.